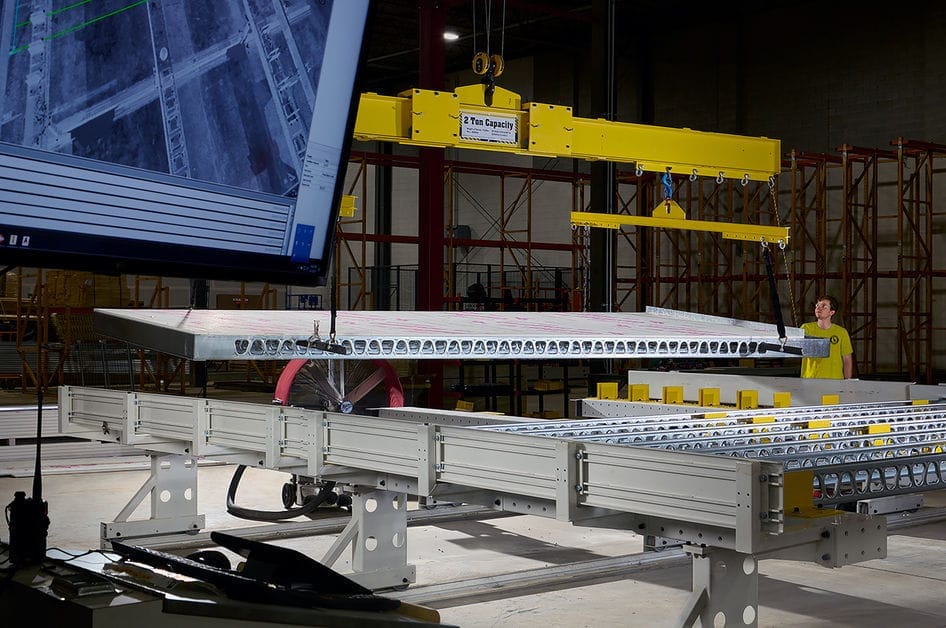
Companies embrace strategies for completing projects on time, within budget
Commercial construction is booming in Northern Indiana with contractors erecting millions of square feet of medical facilities, data centers and warehouses.
They’ve done so profitably, in the face of rising material and labor costs, by turning to novel strategies and technologies like modular construction and a design/build approach to bringing projects under budget and ahead of schedule.
Northern Indiana businesses, school districts and health care systems are hiring contractors to upgrade and expand existing buildings, said Scott West, Tonn and Blank Construction’s vice president of business development.
New construction is on a tear as well with the e-commerce sector commissioning distribution warehouses, cold food storage facilities, data centers that are rising along the Interstate 65 corridor and communities near the Lake Michigan shoreline.
According to Latitude Commercial’s 2023 market report, more than 2.4 million square feet of industrial space was delivered that year alone. The Crown Point commercial real estate brokerage also reported that 2024 brought an even greater influx of space, with about 1.6 million square feet each quarter, due in part to a new Amazon facility.
West said construction growth is driven by the area’s proximity to east-west transportation corridors connecting Chicago’s business hub, but without Chicago’s high property taxes and cost of living.
Building indoors
Drew Peuquet, CEO of Chester Inc., a Valparaiso-based commercial construction firm, said his company has done prefabrication work on an area warehouse, a steel storage facility in Chesterton, a mixed-use building in Valparaiso, and a concrete building in Merrillville.
Price increases have been across the board in construction. It is a daily task to keep up with the increases in steel, wood, concrete and aluminum.”
Hill Mechanical Corp. of Franklin Park, Illinois, recently completed 30 modular health care business projects in the Chicago area, opened an Indianapolis office and has a team devoted to finding projects in Northern Indiana.
“We offer cost and scheduling consistency,” said Kari Holtz, a project executive for the architectural and modular division at Hill Mechanical.
Kevin Comerford, professional development director at the Construction Advancement Foundation of Northwest Indiana, said Tonn and Blank is leading the charge on modular strategies in Northwest Indiana.
An example of modular construction is a doctor’s exam room where the walls, floor and ceiling come together in a factory many miles away.
Tonn and Blank Construction, with headquarters in Michigan City, recently had dozens of such rooms stacked on the floor of their off-site construction facility, waiting to be shipped out to the Franciscan Health Munster acute care hospital.
“We roll out three (10-foot by 12-foot rooms) a day,” said Jack Hudgens, a project manager at Tonn and Blank. “The off-site facility, in operation for four years this June, has done hundreds of rooms and thousands of walls.”
That includes the Franciscan Health Crown Point hospital, the Hammond and Valparaiso YMCA fitness centers, Beacon Health System’s Elkhart General Hospital and Urschel Laboratories of Chesterton.
He said modular construction can be 25 percent cheaper than traditional “stick built” work on the construction site because of the speed his workers can assemble interior rooms and exterior walls, complete jobs and open commercial buildings for business.
“Time is where all the money is,” Hudgens said.
The off-site facility is a climate-controlled 85,000-square-foot building with plenty of room for 25 employees to conveniently organize building materials and operate the technology that shaves months off construction jobs.
They work in ergonomic work spaces on a level shop floor instead of a sloppy open-air work site atop an unfinished building where expensive scaffolding would be required.
Inflation woes
But inflation has eaten into profits, so companies have needed to be creative in the ways they approach projects.
“Price increases have been across the board in construction,” Chester’s Peuquet said. “It is a daily task to keep up with the increases in steel, wood, concrete and aluminum.”
Dewey Pearman, executive director of the Construction Advancement Foundation of Northwest Indiana, said some relief is in sight, but prices will stay higher.
“Some materials have gone down a bit but certainly not to pre-pandemic levels,” he said.
Supply chain issues have pretty much worked themselves out, he said, so companies aren’t seeing increased costs caused by delays.
“But there is a possibility of future disruption given the recent talk about tariffs that could affect the supply chain,” Pearman said.
Those sentiments have kept construction companies looking for ways to reduce costs.
On-site construction
Hudgens gave Northwest Indiana Business Magazine a tour of Tonn and Blank’s assembly line, including an automated router whose operator cuts aluminum-reinforced exterior cladding to the correct width and length, and incises openings for ventilation, plumbing and electrical outlets. In another section, union carpenters assemble wall frames of lightweight steel studs.
“It’s lighter, stronger and doesn’t warp,” he said.
Those frames are joined with custom-designed fusion welders using less heat than arc welding.
“You don’t have to wear a helmet or anti-flash,” Hudgens said. “It has about 10 times the strength of a screw, so this is faster, stronger and doesn’t leave a lump that a screw would.”
Rooms with a 3D projection laser guides placement weld point and screw holes where drywall is attached to the frames, which are assembled into a shell of walls, ceiling and floors with the help of small overhead cranes.
One union carpenter, he said, is “using an iPad to check the dimensions without a drawing and scan a QR code sticker that each completed room gets to document who did work on the room, the process used to make it, and the brand of electrical fixtures and plumbing used inside.”
It also includes a list of 150 check points that inspectors make, stress testing framing welds, plumbing and electrical wiring for potential defects before rooms are loaded on a truck to be shipped to the construction site and hoisted into place.
But other contractors are skeptical.
“It is very popular way to use modular construction because it’s a repeatable format,” said Ryan Kring, vice president of business development for Goshen-based Ancon Construction.
“You have modular home builders in the Midwest, but commercial modular in the Midwest really hasn’t taken off. The cost of shipping is the difference,” he said, adding many modular assembly lines are in the South or on the East Coast.
Expansion made easy
Tonn and Blank also prefabricates modular walls for Family Express convenience stores, fueling and car wash locations.
“This nontraditional construction method for building provides faster speed-to-market, better supports our growth strategy, and allows us to serve our customers sooner,” said Peter Andreou, vice president of development at Family Express.
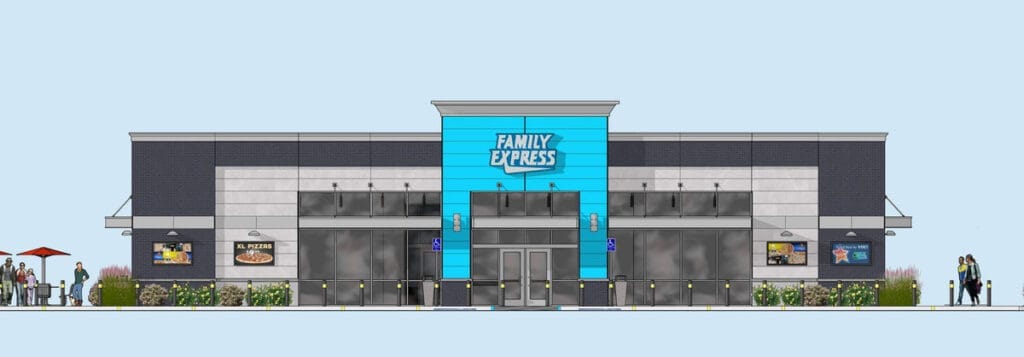
Andreou said Family Express has five projects slated for completion in the second and third quarters of 2025 “with 17 more sites in our pipeline, all utilizing prefabricated modular wall panel systems … a $100 million expansion.”
The company is counting on a prototype that calls for contemporary design to reach its growth goals.
This nontraditional construction method for building provides faster speed-to-market, better supports our <br />growth strategy, and allows us to serve our customers sooner.”
He said reasons for using Tonn and Blank’s modular wall panels include:
- Family Express’ preference for the safer and less stressful work environment of prefabrication.
- Modular construction is quicker.
- The improved craftsmanship of modular construction “gives tighter accuracies and more
dimensionally correct wall panels fabricated in a controlled environment, using lasers. - Modular construction reduces material waste and disruption to the surrounding area by minimizing
noise, traffic and pollution.
“We anticipate installation of these panels to be under one week per site … a reduction of over 85% compared to traditional stick building,” Andreou said.
Design/build strategy
But prefabrication isn’t the only approach to containing construction costs. The design/build model is the go-to method for some companies to bring projects under budget and on time.
Kring said Ancon’s design/build services offer advantages over the customary way of organizing a project. First an owner hires an architect who bids it out to contractors for the best construction terms and costs — only after the design and blueprints are set.
“The traditional way, you don’t know what you’re going to get,” Kring said. “We have a whole in-house architectural staff.
“We partner with the architect right from the beginning, so that way, the construction team is working alongside the architect in a way that makes sure the building is constructable, cost effective, and if the budget becomes high, we can value engineer it.”
Comerford of CAF said other companies aren’t quite sure the model will work for them.
“All contractors have looked into it, but it doesn’t seem too many are doing it and may not until they can figure out the cost/benefit and if there is a market for it,” Comerford said.
But Kring said the method pays off in one significant way.
Traditionally, architectural firms may charge the owner for their services based on a percent of a project’s cost. “We charge anywhere from $5,000 to $20,000,” Kring said.
“The traditional way, you still have a lot of change orders,” he said.
A change order is a modification of the agreed work and cost because of an unforeseen challenge.
“So, if the project is budgeted at $1 million, it typically ends up costing $1.1 million,” he said.
“We don’t have change orders unless the customer changes something. It’s a way to minimize your risk. It’s the true way to do design/build.”
Tonn and Blank offers preconstruction design and cost estimations, as do Hill Manufacturing and Chester Inc.
“We have architects and engineers on staff,” Chester’s Peuquet said. “We can take an owner’s idea and turn it into reality.”
Larson-Danielson Construction Co. Inc. of La Porte started a design division as well.
“We have an in-house designer, Facet Architecture,” said Nick Larson, vice president of business development. “That really lends itself to us being able to control the designs from a value standpoint.”
He said this type of relationship can pay off in more ways than one.
Design/build is nice for an owner. If there are issues … they don’t have to coordinate between their contractor and their architect, playing middle man in a dispute.”
“At times, we’ve seen other architects specify more than what is required, and the owner may not be attuned to that sort of detail,” Larson said. “By controlling the design aspect, we can bring costs down and stay within the owner’s budget and project requirements. As we go through the design process, we then verify that costs are on track.”
He said the design/build process “easily offers savings of 5 to 10 percent if not more,” and frees up valuable time.
“While we are still designing finishes on the building’s interior, our on-site people can get concrete and steel contractors suppliers on board for the building’s foundation sooner,” Larson said.
“Design/build is nice for an owner,” he said. “If there are issues that need to be worked out, they don’t have to coordinate between their contractor and their architect, playing middle man in a dispute.”
What’s next
Larson said incorporating artificial intelligence into design and construction offers future promise.
“Right now, it can only handle simple stuff that doesn’t lead to a lot of efficiency,” he said. “They are quickly becoming more powerful; in the next two or three years, we will probably use it in some form.”
With technology driving more efficiency, commercial construction grows.
“Demand for new construction remains high,” Pearman said. “Industrial construction has ticked down a bit, but commercial and public works is more than making up for that.
“We anticipate 2025 to be flat, relative to last year, but that was a very, very good year for the (construction) industry.” •