By Rick A. Richards
The landscape at BP's Whiting refinery on the shore of Lake Michigan is a Rubik's Cube of pipes, derricks, construction cranes and scaffolding.
Through a mindboggling maze of pipes, hissing steam, narrow roads and steel beams, it's hard to tell where the refinery process ends and where construction on a $3.8 billion modernization project begins. By any measurement, though, it's a massive project, whether it's dollars and cents (the price tag for this project is listed by BP as the largest private investment in Indiana history), or whether it was the use of the world's largest crane to set mammoth vessels in place for the refinery's new coker.
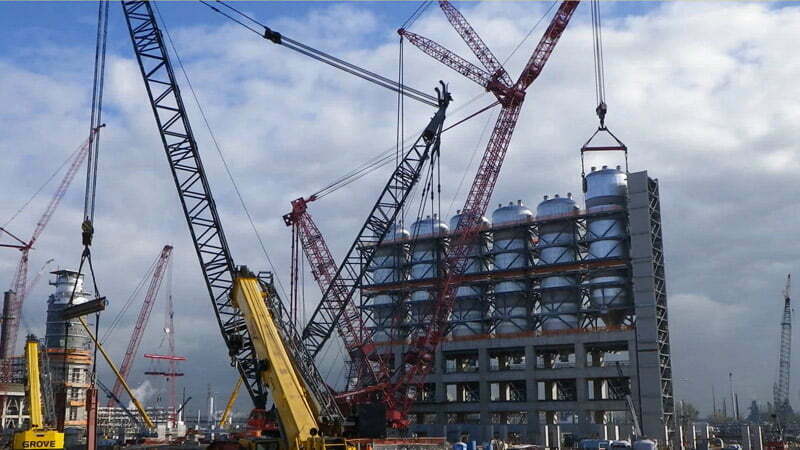
And don't forget the thousands upon thousands of construction workers who began working on the project back in 2008 and won't finish until mid-2013.
Keeping everything on time and on budget is Mike Berna, deputy construction director for the project. His day is filled with meetings with BP officials, safety crews, contractors and local community officials. And through it all, Berna approaches his job with a smile on his face.
“I'm a third-generation refinery employee,” says Berna. “My grandfather and father worked here. I've been a part of it for 31 years. It's extremely interesting to talk about that. In my younger days, the old-timers would come up to me and ask me to swear on my grandfather's grave that things were going to happen as planned. I had to make sure I did well because of the legacy of my father and grandfather.”
Brad Etlin, director of government and public affairs for BP America Inc., says the modernization of the refinery is a necessity in order to keep the 1,400-acre facility operating and preserve its 1,900 jobs.
“It will increase our capability to process heavier crudes, especially tar sands from Canada,” says Etlin. Tar sands have the consistency of asphalt and without the upgrade, BP wouldn't be able to process that resource.
“The headway we've made on this project has been remarkable thanks to the safe and conscientious work of BP employees and several thousand contractors, as well as the continued support from community members,” says Nick Spencer, business unit leader at the Whiting Refinery. “The modernization project is a source of pride for Whiting residents because of the job creation and security it has brought to the region as well as the significant indirect benefits to local retailers and suppliers.”
Etlin explains that the project includes a new coker complex, a crude distillation unit, a gas oil hydrotreater, sulfur recovery facility and modernization of the refinery's water treatment plant.
The heart of the project is the coker facility. It will heat the heavier tar sands crude oil, distilling it into products such as gasoline and diesel. The coker complex has six drums, 30 feet by 125 feet tall, each weighing 793,000 pounds.
From there, material goes to the 12-pipe distillation tower, which works much like a series of coffee filters. The holes in the filter get increasingly smaller and along the way different petroleum products are “filtered” out and sent on their way to the refining process.
“This will give us the capability to process tar sands. It will increase our through product from Canada,” says Berna. But to assemble the coker, BP contracted with Mammoet PTC crane – the world's largest – to set the massive coker drums in place. It arrived on 158 trucks and took 30 days to assemble.
Berna also is in charge of logistics for the project, making sure that contractors from Spain, Italy, the Philippines and from across the United States get their specialized components to Whiting on time.
Every detail has been mapped out, including construction of a 54-acre barge dock on land BP is leasing from ArcelorMittal in East Chicago. When the project is done and BP no longer needs the land, ArcelorMittal will have a new dock.
“This dock was built especially for us, but when we're done, Mittal will thank us for it every day,” says Berna, adding that maintaining the dock after BP hands it over will be Mittal's responsibility. “Before we built the dock, this was just forgotten land. But without it, we couldn't have done this job.”
In addition to the dock, BP built a 47-acre contractor trailer complex and parking area at 129th Street and Dickey Place. It also leases 600,000 square feet of warehouse storage at the Ameriplex at the Port complex in Portage.
But to get components to the dock, Berna had to make sure each one – including the 46-by-166-foot, 1.7 million pound vacuum tower – was built to exacting specifications because each had to fit under bridge spans or through lift bridges along the Mississippi and Illinois rivers, or squeeze down city streets in East Chicago and Whiting in order to get to the refinery.
Other components arrived at the Port of Indiana and were then put on a barge and shipped across the lake to Whiting.
“We had to coordinate around the shipping season on the St. Lawrence Seaway,” says Berna. “We have three more large ships coming from the Philippines and they will start their journey on March 24 in order to get material here when we need it.
“Lots of things are coming from the United States; our steel is coming from Texas and lots of our vessels are U.S.-based. Only the very large vessels for the cokers were not made in the U.S. and that's because they're very specialized,” says Berna. “It was important to be near a port where they could be handled.”
For instance, some of the pipe that has been shipped to Whiting and now sits in a storage lot was 96 inches in diameter. By the time the project is finished, more than 1.4 million feet of pipe will be installed, each section welded by hand.
“This is all specialty carbon steel pipe with a stainless lining,” says Berna. “It was brought over from Spain. This isn't just the logistics of getting material on the hook for the crane to lift it into place; it's the logistics of every little piece along the way. Our hopper barges go up the Mississippi and Illinois rivers from Louisiana, and to get past the bridge in Lemont, Ill., nothing could be taller than 22 feet.” That's why the barges sit a bit lower in the water.
As the project moves ahead, Berna has to make sure that the daily production of 7.5 million gallons of gasoline and 1.25 million gallons of jet fuel isn't interrupted. That's why special racks called modules have been built that can be lifted once and then by using a series of jacks, moved into place up to 600 feet away. The racks – more than 600 of them – carry the pipes and wiring that will be used in the distillation process of the heavy crude. They are built off-site rather than built a piece at a time because it's safer and causes less disruption in the refining process.
In addition to gasoline and jet fuel, the BP refinery also produces naphtha, gas oil which is used to produce low-sulfur diesel and jet fuel, and residual material from which petroleum coke for power plants and asphalt for road construction is refined. The BP Whiting refinery produces about 8 percent of the nation's asphalt.
Once the new equipment is in place and operating, older equipment will be taken offline and removed. Berna says the new machinery will improve efficiency and productivity at the refinery and reduce both water and air emissions.
As the project continues, Berna says he's especially proud of the safety record the refinery has during the project. Only a few minor injuries have been reported, but he credits that to the workers and the community.
“We have a meeting every day with our security, EMS and fire and with representatives of the community. We let them know where we need to route people and materials that are going to close roads,” says Berna. “If there is an emergency, fire and EMS need to know exactly where they are going and how they're going to get there.
“We send out e-mails to all adjacent businesses that may be affected,” says Berna. “We also keep in touch with Whiting, East Chicago and Hammond police departments to let them know, too. Constant communication is an absolute key.”
Etlin explains that the communities have been eager to cooperate because they realize the importance of the project to their future.
“This project is very important to the local economy,” says Etlin. “There are hundreds and hundreds of local businesses that benefit from this project. In addition to 1,900 employees on site, there are up to 3,500 contractors working here. Engineering assistance has come from BP's North American headquarters in Houston, and from its corporate office in London.
“They frequent local restaurants, local retailers, suppliers and services. It's having a massive impact. Even when the modernization is complete, we're going to require thousands of contractors for maintenance.”
When BP made the decision to modernize the refinery, Etlin says Whiting breathed a sigh of relief. “This modernization will keep the refinery viable for another 30 or 40 years. People are very proud to be here and working on this project. There are no other projects like this. It gives us the flexibility to process whatever we want.”
In fact, when BP completes the modernization, it will sell its refineries in Texas City, Texas, and Carson, Calif. That will leave BP with only three refineries in the U.S. Besides Whiting, the others are in Cherry Point, Wash., and Toledo, Ohio.
BP Whiting History
1889 – Construction of a refinery begins on 235 acres.
1890 – First shipment of 125 tank cars of kerosene is shipped.
1913 – Whiting Refinery engineers discover that by using pressure and high temperature, they can double gasoline output from each barrel of crude oil, a discovery that becomes vital during World War I. Production goes from 2 million barrels of gasoline in 1914 to 12 million barrels in 1918.
1923 – Refinery engineers discover that by adding tetraethyl to gasoline it improves the performance of automobile engines.
1941 – Four days before the bombing of Pearl Harbor, research at the refinery leads to the discovery of a process that can make high-grade aviation fuel from low-octane naphtha.
1959 – Construction is completed on the second of two crude oil pipe stills that can distill 140,000 barrels of crude oil a day.
1972 – Whiting's No. 4 Ultraformer begins operations. It is a process where molecules of gasoline are “reformed” to produce high-octane gasoline that is lead-free.
1977 – The refinery establishes an all-time production record of 504,000 barrels of crude oil in 24 hours.
1993 – The Distillate Desulfurizer Unit is built to provide low-sulfur diesel fuel.
1999 – Whiting becomes part of the newly merged BP Amoco Corp.
2006 – Whiting Refinery announces a massive modernization project.
2008 – After obtaining the necessary permits, construction begins.
2013 – Whiting Refinery Modernization Project is scheduled for completion.