Stakeholders take steps to ensure steelmaking has solid future in Indiana
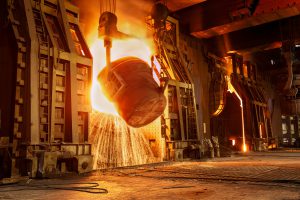
With about 27% of the nation’s steel produced in the Hoosier state, Indiana is the country’s steelmaking capital.
“Indiana is the largest state on an annual basis for steel production, and it has been for decades,” said Timothy Gill, chief economist of the American Iron and Steel Institute.
For more than a century, the steel industry has been a big player in the Region’s economy, and for good reason.
The iron and steel industry directly employs 28,000 workers in Indiana, Gill said. That’s a total economic impact of more than $12 billion, factoring in suppliers and workers’ spending.
Steelworkers earn an average of $101,144 per year in wages and benefits, according to an AISI fact sheet.
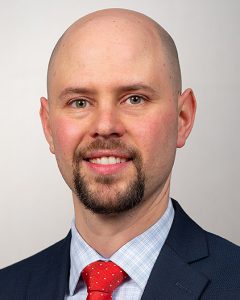
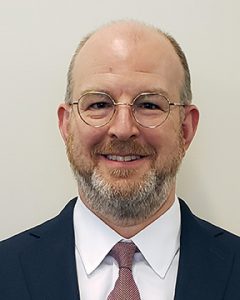
“You might as well turn off the lights and roll up the curbs” if the steel industry ever disappears from Northwest Indiana, said Karen Lauerman, president and CEO of the Lake County Economic Alliance.
Micah Pollak, director of the Center for Economic Education and Research at Indiana University Northwest, offered data specific to Lake, Porter and La Porte counties. The number of jobs in the primary metal manufacturing industry in those three counties rose from 560,428 in 2002 to 745,274 in 2021.
Total wages rose from $951 million to $1.3 billion over the same period, he said.
“When I came here in 2012, the outlook for steel was not particularly bright,” he said.
Evolving industry
Some of Pollak’s predecessors published a study in spring 1993: “Dinosaurs on the Lake? Steel in the Next Decade.” That study decried the lack of major technological improvements among integrated steelmakers.
But that’s no longer the case, experts say. Pollak is now convinced the steel industry’s prospects in the Region are improving, too.
“The perception of steelmakers (and) of people in the steel industry, they have an old perception of what steel is all about,” said Patricia Persico, senior director of corporate communications at Cleveland-Cliffs. “It is a high-tech industry.”
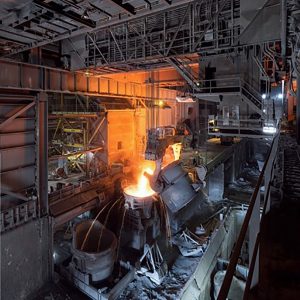
Workers now need an understanding of metallurgy, data analytics or other specialties.
Gill said the industry is ever changing.
“There’s been a lot of merger and acquisition activity both upstream and downstream,” he said. U.S. Steel purchased Big River Steel in Arkansas in 2019, and Cleveland-Cliffs bought ArcelorMittal, including its Indiana Harbor and Burns Harbor mills, in 2020.
Companies have been acquiring fabricators and processors, too.
Since Cleveland-Cliffs acquired ArcelorMittal, it has been on a spending spree in Northwest Indiana.
“We quickly jumped into action,” said Traci Forrester, the company’s executive vice president of environmental affairs and sustainability.
At its Burns Harbor plant, the steelmaker has spent $160 million for two new walking beam furnaces and $170 million for the boiler house and powerhouse to improve energy efficiency.
At its Indiana Harbor operation — the largest integrated steel mill in the U.S. — Cleveland-Cliffs spent $100 million to reline its No. 7 blast furnace.
When blast furnaces are relined, not only is their functional life extended, but they’re also updated and modernized with the latest and greatest technology, Forrester said.
Persico said water treatment plants have been improved.
“You can see the dollar amount is substantial, and we’re talking within the first two years of acquisition,” she said.
Forrester said Cleveland-Cliffs engineers are reviewing everything at both plants, as well as the Tek and Kote facility in New Carlisle with an eye to improvements.
“I think it’s going to be the same approach, (because) we’re all about being proactive,” Forrester said. “It’s really about quality and consistency for Cliffs.”
Tek and Kote gets its steel by rail from Indiana Harbor and Burns Harbor. Gary and Burns Harbor plate operations get steel from both places, too.
Steel production is an increasingly high-tech operation.
“I see basically a continuous effort to produce steel in our blast furnaces,” Forrester said. “I think the future of steel is strong in (Northwest Indiana).”
She said Indiana is an important location for Cleveland-Cliffs.
The company employees 7,000 workers, not counting vendors and suppliers, in Northwest Indiana.
U.S. Steel also is committed to remaining a major part of Northwest Indiana’s economy.
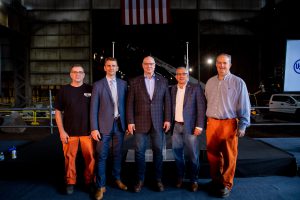
“There are very exciting things coming to U.S. Steel in Gary,” said Amanda Malkowski, media relations manager. The company is spending $60 million on a new pig iron caster.
The pig iron caster will use iron ore from the company’s Minnesota operations. The product is expected to supply up to half of the ore-based metallics needs for U.S. Steel’s Big River Steel Works. The new caster is expected to generate 25 new jobs when it begins operating in early 2023.
“Gary Works is U. S. Steel’s largest manufacturing plant, and its role in the company and in this community is significant,” said Daniel Killeen, vice president of Gary Works, during the company’s announcement of the project. “Knowing that the nearly 4,000 employees at Gary Works are not just contributing here, but we now get to utilize our blast furnace efficiency to contribute to the company’s new, most environmentally friendly operations at Big River Steel Works, is something we’re excited about.”
Supply chain disruptions were a factor in the company’s decision.
“Mined, melted and made in America has always been important to us, and recent world events have demonstrated how critical self-reliance is,” said David Burritt, president and CEO of U.S. Steel, during the Gary Works investment announcement. “This investment at Gary Works, to create the necessary material for our lower-emissions electric arc furnaces, is the perfect example of combining the best of integrated and mini-mill technologies.”
Sustainable goals
Both U.S. Steel and Cleveland-Cliffs are investing heavily in efforts to meet sustainability goals aimed at reducing the companies’ carbon footprint.
A $3.5 million grant from the U.S. Department of Energy is funding a University of Illinois study on capturing and storing carbon at Gary Works. It seeks to determine whether it’s feasible to use concrete products to mineralize an estimated 5,000 metric tons of carbon dioxide annually.
“You need carbon to make steel, (because) it’s never been carbon-free,” Forrester said. But the company has a study underway at Burns Harbor to determine feasibility of capturing carbon.
The technology exists for the oil and gas industry, but it hasn’t been proven yet for blast furnace gases, Forrester said. The study also must determine whether the project would truly be a reduction in overall emissions.
Cleveland-Cliffs’ goal is to reduce carbon emissions by 2 million tons annually.
Flares burning off waste gases won’t disappear from the Region’s steel mills. But air emissions have been reduced in recent years.
“We don’t like to think of them as smokestacks but steamstacks,” Forrester said, because most of what appears to be smoke is really steam.
Cleveland-Cliffs also is working with vendors at Burns Harbor and Indiana Harbor to get them to help lower air emissions with the work they do at the mills.
“It’s as simple as ‘Hey, guys, put some covers on your trucks,’” Forrester said. “It’s a partnership effort, really.”
The company also works with its customers, including taking pre-consumer scrap from downstream processors and melting it in basic oxygen furnaces to make additional steel.
“We work with the customers and help them meet their sustainability goals,” Forrester said.
Finding innovations
Both companies are conducting research and development for new types of steel as well. In addition, ArcelorMittal’s sale of its Region operations to Cleveland-Cliffs excluded the ArcelorMittal global R&D facility in East Chicago.
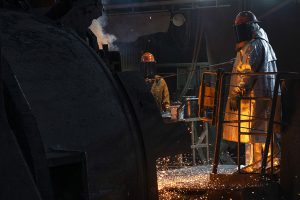
That center continues to serve ArcelorMittal operations elsewhere.
As customers’ needs change, so does the steel produced by steelmakers.
Cleveland-Cliffs and U.S. Steel are heavily dependent on the automotive industry.
Forrester said to help the automakers meet corporate average fuel economy standards, domestic steelmakers have developed strong, lightweight steels that are supplanting aluminum. As automakers shift toward electric cars instead of internal combustion engines, lightweight steel becomes important in extending electric cars’ range.
“These are very highly technical studies and experiments,” Forrester said. Developing a new steel for a particular application can take months or even years.
“It’s chemistry, it’s physics, it’s all of the above,” she said.
Pollak said, as the steel formula changes, employees’ skills also need to.
“In general, employment in steel has been declining in Northwest Indiana,” he said, a direct result of increasing automation in the industry.
Steelmakers now are controlling the machines that control other machines, requiring “more training, more education, more experience,” Pollak said.
“It’s still an excellent industry to be in” because of the high pay, he said.
Gill sees that change in the workforce, too.
“The jobs in a steel mill these days are very, very different from the jobs that were there a decade ago,” he said. “The nature of the jobs has changed,” with workers now more likely to be in a control room.
Lauerman said the Steelworker for the Future program at Ivy Tech Community College used billboards, which showed a starting salary of $90,000 annually to attract attention.
“If I knew then what I do now, I would have done something different,” she said. “They’re actually reinvesting in the workforce; they’re actually investing in the Region.”
Pollak said primary metal manufacturing — predominantly the steel industry — now accounts for 6.3% of jobs but 25% of wages in Lake, Porter and La Porte counties. That compares to 7.6% of jobs and 30% of wages in 2002.
Steel’s clout
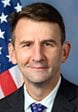
U.S. Rep. Frank Mrvan of Highland recognizes the importance of the steel industry in Northwest Indiana. He is co-chairman of the more than 100-member Congressional Steel Caucus, a nod to steel’s importance in Indiana’s 1st Congressional District, which he represents.
“It’s a big part of my body of work,” he said.
Mrvan said it’s important for the country to make its own steel.
“We have to produce steel domestically in order to produce our tanks, our ships, our planes,” Mrvan said. Russia’s invasion of Ukraine this year drove home that point.
When Mrvan announced his endorsement by retiring Rep. Pete Visclosky, Mrvan chose a United Steelworkers of America union hall to share the news. Having the union’s endorsement was another big boost for his campaign.
Once in Washington, Mrvan quickly advocated for the domestic steel industry. He has testified before the International Trade Commission six times about other countries circumventing trade laws aimed at ensuring a level playing field for industry competitors.
“American workers have already lost their jobs” when the ITC rules on a trade case, Mrvan said.
As former North Township trustee in Lake County, Mrvan saw the impact of foreign trade on Hoosiers. Members of Local 533 were laid off from an aluminum plant.
“Families here absolutely locally lost their jobs,” he said.
As congressman, Mrvan helped ensure the infrastructure bill passed by Congress this summer had a strong Buy American Provision.
“Those bridges that we need to replace in Indiana? They will be made with American steel,” he said.
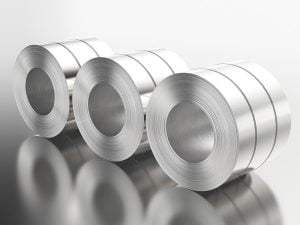
Ripple effect
Jobs at Northwest Indiana steel mills are important to the local economy, but so are other jobs.
“There are thousands of jobs that are reliant on downstream industries,” Mrvan said, during an interview at the Corner Café in Griffith.
Lauerman said, when steel is doing well, that means restaurants do well.
Mrvan said Northwest Indiana needs a vibrant manufacturing base to send kids to college, buy homes and more.
“The steel industry, they’re working extremely hard, and they’re producing a lot of steel,” he said.
Lauerman said a strong steel industry means contractors can build, which boosts employment among the skilled trades.
Lauerman pointed to a building owned by Crow Holdings Industrial at AmeriPlex at the Crossroads in Merrillville. It houses three businesses:
- Quality Pasta provides 70 jobs and occupies nearly 90,000 square feet.
- Turbonetics employs 100 and occupies 65,500 square feet.
- Midwest Truck and Auto, employs 150 people and occupies 125,000 square feet.
Then there’s the 1 million-square-foot building being built by Arco/Murray at Silos at Sanders Farm in Merrillville, which will require 4,000 tons of steel. About 300 construction workers will construct the building, she said.
Steel also is important for Union Tank railroad cars, BP’s Whiting Refinery, seating manufacturer Lear and others, Lauerman said.
A thriving steel industry also helps Lauerman and Don Koliboski, the Lake County Economic Alliance’s vice president for economic development, lure companies to the urban areas in Lake County.
“There are ancillary businesses, many of them who rely on that, that we’ve brought here,” Koliboski said. “Steel is still a very critical component.”
At national conferences, it’s easy to sell Northwest Indiana by mentioning the largest integrated steel mill in the country, BP’s Whiting Refinery, the nearby Ford plant and other industrial giants, Lauerman said.
“We’ve been touting this for years,” she said. “That’s just one more way the steel industry is helping to draw new jobs, to draw new investment.”
Lauerman said there are opportunities for the logistics industry to move steel made in the Region.
“These businesses require conveyor systems, machinery that is made from steel,” she said. “I’m pretty proud, and actually we’re pretty lucky, because we have our legacy industries of oil and steel.”
Click here to read more from the October-November 2022 issue of Northwest Indiana Business Magazine.