Manufacturers, educators and community partnering to train workers
Many Northwest Indiana manufacturers are facing a dilemma: not enough skilled workers to operate the sophisticated equipment on today’s factory floors.
Training is the answer. But manufacturers are busy turning out products to service their customers. They don’t have the time or ability to develop full-scale training programs, especially those that involve only a few workers at a time.
To meet the need for more training, the Indiana Department of Workforce Development launched the Skill UP grants program a year and a half ago. This initiative brings together workforce, education and industry professionals to come up with targeted strategies for meeting current workplace demands.
Manufacturing Key Engine of Indiana Economy
That’s paramount in a region where manufacturing is expected to continue being the key economic engine, according to Allison Bertl, Regional WorkOne Business Services Manager at the Center of Workforce Development (CWI) in Valparaiso. The manufacturing industry contributed more than $12 billion, or about one third, of the region’s Gross Regional Product in 2013.
Bertl says about 60 percent of jobs in the region are in manufacturing, and they’re relatively high paying, with median earnings of about $18 an hour. Many of the jobs are in high-demand occupational areas that require specialized certifications in addition to a high school diploma.
Skill UP is making a difference for Northwest Indiana manufacturers by “upskilling” existing workers and those who are unemployed. Bertl says, “Northwest Indiana has a need to replace those who are retiring as well as to fill new positions in manufacturing that are coming into the region. We’re focusing on under-skilled or unemployed workers.”
Employers Pinpoint Skill Shortages
The CWI facilitated several strategy sessions with industry partners in the region to pinpoint workforce training priorities. Through these strategy sessions, employers came up with three primary areas where the skill shortages were most prevalent. Following that, targeted strategies were developed and implemented to address these challenges.
“The most unique thing is it’s a great example of workforce, educators and industry coming together to address skills shortages of our workforce and develop solutions,” Bertl says.
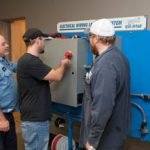
The three core areas forming the foundation of the Skill UP program are: production, machining and industrial maintenance. Most of the training has taken place at Ivy Tech campuses across the region. Kathy Neary, Ivy Tech Workforce Alignment Consultant, collaborates with manufacturers to train workers in credit and noncredit programs.
A certified production technician program is offered for those coming into the workforce without desired skills, Neary says. “It gives them the basis for jobs in manufacturing.”
T&B Tube Co. in Gary hired a graduate of the certified technician program a year ago and is happy with the results, according to Kevin Barker, operations manager, and Rachel Trotman, human resources generalist. The company also used grant funding from WorkOne Northwest to train the new employee on the job.
By going through WorkOne Northwest to find the right employee, T&B Tube was spared the time required to go through stacks of resumes and the cost of drug screens and background checks for employees who often don’t pan out.
T&B Tube is a family owned and operated company that has supplied cut-to-length steel tubing for more than 30 years. The mill recently relocated from South Holland in Illinois to Gary when the state of Indiana, the City of Gary and MIPSCO offered incentives to make the move. The company was looking for a larger space to expand operations and add jobs. Troutman notes that, before the move, most employees were already Indiana residents, including company president Jack Jones.
Barker says the career prospects at T&B Tube are good. Workers make an average wage of about $15 an hour and receive a generous benefits package plus opportunities for advancement and tuition reimbursement. He’s working with Neary of Ivy Tech and Bertl of WorkOne Northwest to bring together several companies in Gary and the surrounding area that need to train industrial maintenance workers. He says it’s one of the hardest positions to fill right now because it requires specialized skills to operate sophisticated electronic equipment.
New Skills in Demand
CWI’s Bertl says a shift has taken place in skill sets of industrial maintenance technicians, who formerly had skills in either mechanical or electrical systems. “They’re much more valuable to employers if they have a wider set of skills that include both mechanical and electrical systems.”
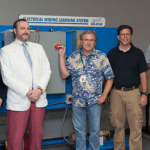
A collective approach to training was modeled in a pilot program recently completed in Pulaski County. Five manufacturers came together to train a total of seven employees through an 18-week course designed and developed by Ivy Tech educators. Training space was offered in kind at the Winamac Coil Spring plant.
Neary says, “What’s unique is it’s very skills heavy training. There are some lectures but a lot of the work was (done) in a lab.”
The Pulaski County program was designed to meet newly released industry recognized credentials from the National Institute of Metalworking Skills (NIMS) in the area of industrial maintenance.
“These credentials are designed to ensure participants have the necessary skills to be proficient on the job,” Bertl says. “Our Ivy Tech partners were instrumental in working to ensure our region could be one of the first in the state to offer these newly released credentials.”
Nathan Origer, executive director of the Pulaski County Economic Development Corp., was a key player in bringing industrial maintenance training to the area. Origer says the area is sparsely populated and, at the same time, is a hub for manufacturers ranging in size from Braun Ability, with more than 1,000 employees, to smaller shops with a half dozen employees.
“Manufacturing has always been a core part of our economy,” says Origer, noting that the once predominantly agricultural area has generated a workforce with solid mechanical skills. “Relative to the rest of the region, Pulaski County has a low unemployment rate and is in need of skilled employees to fill existing jobs.”
Origer says workforce development programs are driven by employer needs. “We’re taking a long-haul view in trying to build a talent pipeline in the area,” Origer says.
Chad Huber, vice president and operations manager at Winamac Coil Spring, is responsible for hiring and training employees. “What we see happening is we have a pretty loyal workforce. A lot of people have been with company 30 to 40 years and will be retiring. The younger generation has less hands-on skills.”
Huber says the concentrated training program was made possible through a partnership of small manufacturers with similar needs. “It’s been fun working with the member companies. All of us are starting to see the need to pull young people into manufacturing.”
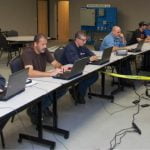
Winamac Coil Spring has already seen a return on investment in terms of increased capabilities of the employee it put through the training. Huber says the employee has demonstrated the ability to apply what he’s learned in real world situations.
Winamac Coil Spring is a family owned and operated company founded in 1948 by Huber’s grandfather. It has grown into a major spring supplier for customers worldwide, with its products in everything from race cars to refrigerators. Its major clients are in farm equipment, sport utility and recreational machine manufacturers.
Danielle Dacanay, human resources manager at the GAF manufacturing plant in Michigan City, says the industrial maintenance training program is a good fit with the company’s belief in investing in employee development. Founded in 1886, GAF has become North America’s largest manufacturer of commercial and residential roofing.
“One of the values at GAF is people,” Dacanay says. “Our net goal is to continue to prepare people with opportunities to grow within the company.
“Training allows people to grow into higher–level operator positions. It sets them up with higher skill capabilities to fit into roles that require leadership, trouble shooting and decision making.”
According to Dacanay, GAF has traditionally separated the jobs of mechanical and electrical maintenance but is seeing the industry shift into having one employee with the skills to do both.
Manufacturing industry jobs are projected to become increasingly concentrated in Northwest Indiana compared to the rest of the country, according to Bertl. With the increase in manufacturing occupations in the region and the ongoing evolution of manufacturing technologies, coordinated approaches to training such as Skill UP will continue to be necessary, Bertl says.
“At a time like this, when unemployment is low and job demand remains high, it’s critical that we continue to align and deploy strategies and resources collaboratively across the region in an effort to respond to and prepare for our industry demand.”
Click to read more from the Fall 2017 issue of Northwest Indiana Business Quarterly.