Higher education works with companies as more automation creates need for specialized workforce
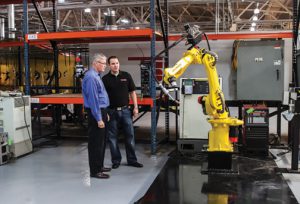
In some economic development circles, Indiana has gained notoriety for its manufacturing prowess.
Experts say the reputation is well earned as institutions and advocacy groups take steps to preserve the sector and ensure it endures well into the future.
Technological adoption is one approach that has met with success, and with the pandemic, more emphasis has been placed on autonomous operations. Experts in the field lend insight into the past, present and future of such advances in manufacturing.
Dan Keller, sales manager for Tri-State Automation in Hammond, is one voice in the manufacturing community whose no stranger to automation. Talk to him for a few minutes and you can hear the passion for his family businesses — Tri-State Industries and Tri-State Automation — shine through.
He said Tri-State Industries’ legacy, which was founded four decades ago, is of an early adopter of automation. As the steel manufacturing industry became increasingly more competitive, the company pursued an advantage through lean manufacturing principles.
In that vein, the company examined internal processes with the goal of automating anything that made sense. Since welding was a substantial part of the work done on site, robotic welding was a natural place to start.
Ultimately, Tri-State Automation was born from that endeavor. They realized that many companies were encountering similar challenges in automating their processes.
Today, Tri-State Industries is a contract robotic welding manufacturing company serving the needs of small- to medium-sized manufacturers. According to Keller, the two companies’ missions are related but distinctive.
“For example, if you wanted to outsource your welding and your manufacturing process to a company like Tri-State Industries to have it robotically welded, we can do that for you,” Keller said. “Or if you’re more interested in actually automating the process internally, that’s where Tri-State Automation would come in.”
To that end, he said Tri-State Automation has partnered with some large robotic manufacturers such as Yaskawa Motoman, OTC DAIHEN and FANUC. They also can do custom systems as well as refurbished units.
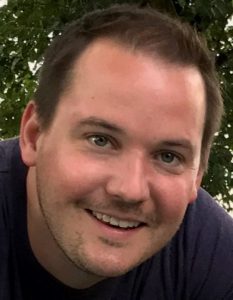
Keller credits Tri-State Automation’s success to the early struggles of its sister company. They were trailblazers and visionaries in one respect.
“When we started (Tri-State Industries), there was no real robotic integration company in the Chicago area,” he said. “We struggled to do it internally and learned a lot by utilizing used robots.”
The company would purchase old robots and try to repurpose them.
“We first did that about 22 years ago, and now we’re up to 17 different systems,” Keller said.
To understand the big picture and how the company helps modernize facilities, Keller frames the story with some data and qualitative markers. For one, most customers see a return of investment in as little as 18 months.
“We can usually double or triple the output for customers,” he said. “So, you know, it might take your average welder a minute and a half or three minutes to weld a part, where a robot can do that in 30 seconds because they move very, very quickly.”
Other factors are at play, too. Repeatability is one. For example, a welder might be feeling good one day and not so great the next. In other words, a robot can ensure more predictability in terms of quality.
Keller said, in this way, humans — who are susceptible to infections like COVID-19 — are no match for robots in certain contexts. However, experts aren’t suggesting the human element is or will be completely removed from the equation.
Retraining workers
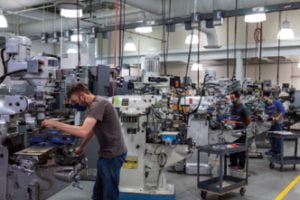
Ivy Tech Community College’s Warsaw campus is skilling up the next generation of manufacturing workers with its vocational training options.
There is a shortage of skilled employees in manufacturing in Indiana, experts say.
The education provided by Ivy Tech gives students the knowledge needed to succeed in a modern manufacturing environment.
Enter Tom Till who is director of Ivy Tech Community College’s Orthopedic and Advanced Manufacturing Training Center. It is a 20,000-square-foot facility in Warsaw, which is the self-proclaimed orthopedic capital of the world.
Ivy Tech’s facility offers programs and training for individuals and organizations, and serves as a vital resource to the Region’s students, employers and businesses.
Till is equipped to lead the charge, because he worked in the industry. As he explained, he and his peers saw the writing on the wall. Representatives from the Warsaw area’s orthopedic giants came together with a singular focus about a decade ago.
“These companies that were normally competitors with one another worked as partners with OrthoWorx and Ivy Tech to develop a program to address a common problem: where do you get enough skilled help to fill the jobs and to keep the industry as a whole healthy,” Till said.
He said Ivy Tech answered the call.
“Ivy Tech Community College’s Warsaw site started a noncredit, 200-contact-hour CNC machine training program so that we could get people skilled up and qualified to take on much-needed roles as CNC operators,” Till said. “We projected a shortage in the industry as far back as 2011 due to CNC retirement patterns and knew our community needed us to train a good base of people to backfill those positions.”
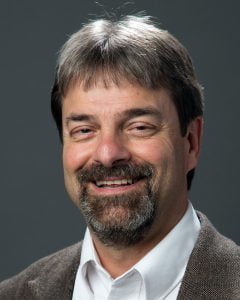
Each student’s academic path and goals will vary, and that’s to be expected, Till said.
Some students may take a few classes and be on their way, while others may seek additional training and complete an associates degree. The classes are designed to be cumulative and provide a real-world education.
As manufacturing environments become more automated, Ivy Tech has evolved by offering its Advanced Automation and Robotics Technology program, which can lead to a certificate or a degree.
Either way, the job outlook is bright, given where the industry is headed.
“Our AART graduates program robots and develop automation systems,” he said. “The cost of automation is coming down significantly, (and) the ability to have machine vision and for machines to be able to see and make decisions based upon what they see is a whole lot better than the vision systems of years gone by.”
La Porte Co. Career & Technical Education at the A.K. Smith Career Center is reaching students even younger. The program serves seven high schools within the state, providing educational opportunities within multiple disciplines.
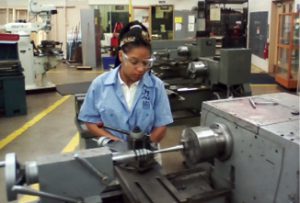
The Modern Machine Technology program, a curriculum developed in consultation with regional business and industry, prepares students for entry-level employment in the metal working and manufacturing fields. High-tech laboratory experiences give students hands-on opportunities to work with engine lathes, milling and drilling machines, and computer numerically controlled (CNC) machines.
The course work includes machining fundamentals, applied mathematics, introduction to print reading, assembly, pneumatics, and CAD and CAM. Additionally, students can earn dual college credits from Ivy Tech and leave high school qualified for an entry-level position in the high-demand precision machining and manufacturing industry.
Chris Smith, Modern Machine Technology instructor at the A.K. Smith Career Center, is proud of the legacy they’ve built in the past decade. Smith worked in a machine shop before joining the center about eight years ago.
He said the program gives students a taste of the real world — a leg up, especially for indecisive high-schoolers. The two-year curriculum starts junior year in high school, and involves both lectures and practical applications. It produces about 20 graduates a year.
‘We’ve grown the program to where we have industrial-sized CNC milling machines,” he said “The idea is for them to be able to work in small groups, or individually — whatever the project calls for — and get familiar with the machines.”
They want students to maximize their capabilities, Smith said.
Smith said the concepts really come alive in this environment. He attributes that to the project-based learning approach.
But the proof is really in the student success stories. According to Smith, it’s all about timing.
“That’s our priority … to make sure every kid graduates first, and then, if everything is going well, then we can introduce them to the industry and get them out there and maybe give them some work experience,” he said. “Our hope is that we can get them doing well enough at school that they can step away and work for a few hours a week in the industry.”
Purdue University Northwest’s College of Technology works with the manufacturing sectors in Northwest Indiana to provide no-cost training to those seeking to upskill. A grant received in late 2019 from the U.S. Department of Commerce makes the program possible.
“This mechatronics technician training provides incumbent workers with 16 weeks of training that covers electrical, mechanical, and PLC components and systems,” said Niaz Latif, dean of Purdue University Northwest’s College of Technology and executive director of the Commercialization and Manufacturing Excellence Center.
Additionally, the PNW College of Technology works directly with WorkOne and the Center of Workforce Innovations to train job seekers in advanced automation maintenance, through their Electrical Maintenance Technician Training. Latif said this training aids in building a pipeline of skilled workers who can troubleshoot and maintain advanced automation equipment.
In this way, Purdue is leaning into the future. The same can be said of its Commercialization and Manufacturing Excellence Center, which is assisting entrepreneurs with fundamental training, including robotics.
“By providing this early introduction to advanced automation, we feel the founders will be aligned with changes in industry towards automated systems,” Latif said.
Advocacy partners
Advocates for manufacturers have worked in partnership with the education community to guide training programs to ensure they continue meeting the sector’s needs.
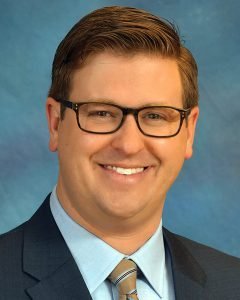
Andrew Berger, senior vice president of governmental affairs at the Indiana Manufacturers Association, said the state has a vested interest in talent development.
Put simply, Indiana is a manufacturing powerhouse and that means there’s a lot to be gained, he said.
“It’s the largest employment sector (in the state) by (a) significant margin and that means we have a lot of eggs in the basket so to speak,” he said.
He also said Indiana has produced many home-grown successes and has attracted companies to locate their headquarters here.
However, while the manufacturing sector is robust, investment in technology can be lacking.
“We have a little bit of a tough tax code when it comes to capital investment, and we have personal property taxes that are high compared to other states,” Berger said.
The fact that Indiana lacks the workforce with the skills necessary to immediately work with or help develop new technologies only compounds those underlying issues, he said.
Berger said manufacturers who successfully attract and retain talent must also scale up their investment in innovations. He offers an assembly line as an example.
“Companies often have to comply with safety and environmental regulations, but automation also allows you to be more efficient,” he said.
This is especially true in the context of COVID-19. He’s heard from IMA members that the labor market is especially tight right now.
For instance, he said workers might need to self-quarantine because they’ve come in contact with a person who tested positive for the coronavirus or they don’t have reliable child care. These realities likely will continue to weigh on the industry, which makes automation even more essential to operations.
Although change does not come about overnight.
“These types of things take a lot of capital investment and a lot of planning,” Berger said.
Click here to read more from the October-November 2020 issue of Northwest Indiana Business Magazine.