From behind the scenes, Region experts find better solutions to advancing many industries
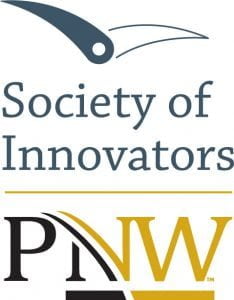
Together, their ideas have improved lives, protected market share, killed germs and allowed virtual hands-on learning.
Their achievements were celebrated at an induction luncheon in November. The annual gathering brings together business and community leaders from across the Region to celebrate the spirit of creativity and ingenuity of innovative individuals and teams across all industries and backgrounds.
Here the five inductees share their stories of perseverance and success:
Level Up
United Way of Northwest Indiana predecessor Lake Area United Way built the infrastructure for true collective impact and serves as the backbone organization for helping low-income working families. ALICE is the acronym for asset-limited, income-constrained, employed.
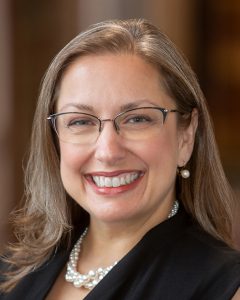
Proulx Buinicki
In Lake County, that’s 29% of families. In Porter County, it’s 27%.
Andrea Proulx Buinicki, vice president for workforce initiatives at the Center of Workforce Innovations, was with United Way, helping guide the Level Up program in Lake County at its inception. She’s still involved but in a different role.
Jessica Callard, who began with United Way in August 2020, became team manager for the program in February.
With the merger of Lake Area United Way and United Way of Porter County into United Way of Northwest Indiana, the Level Up program will expand into Porter County, Callard said.
“So many people who work in one county live in another,” she said. “I think (the merger) will just deepen our ability to help them thrive.”
Level Up is the culmination of numerous listening sessions and community impact groups. One work group suggested a pilot to help ALICE families, who don’t qualify for a lot of federal assistance, Proulx Buinicki said.
The goal is to provide better-paying jobs. Getting there might require skill development, training or certification, but the person can’t take off work to do it.
The family also might need quality, affordable child care for work or school or training, she said.
“We work with these families in order to help them set goals for employment, find appropriate training, find appropriate funding for that training, to access child care and to access services in the community that are available to them that they did not know about,” Proulx Buinicki said.
It’s a rewarding experience for the United Way team as well as for the clients they serve, Callard said.
“Every day is really inspiring,” Callard said. “Their determination and grit to achieve their goals — it’s something every day.”
Proulx Buinicki said, in the Region, many people are working hard but are one emergency away from disaster.
Family navigators Talisa Rogers-Hall and Grace Morin also are named in the Society of Innovators team award.
“They are accountability partners, they are researchers, and they are cheerleaders,” Proulx Buinicki said.
“They are proactively engaged with every single client.”
Callard said Level Up is a team effort.
“Everybody has a gift to share,” she said.
The original goal was to help 10 families access better-paying jobs and support them through the process. The initial thought was that this would be a sequential process — get a job, then get financial management skills.
The team soon realized these two processes needed to happen together.
ALICE families struggle with budgeting, credit and debt. “They needed to have some resources, some education and some coaching,” Proulx Buinicki said.
Funded through grants, financial wellness navigators at organizations that already specialized in those skills were enlisted.
“So many of our clients, their goal is to own a home,” Proulx Buinicki said. Several have bought a new home since 2019.
They had to get their credit in order, make difficult choices about savings and adjust spending accordingly, she said.
New steel
Corporate average fuel economy standards are pushing carmakers into finding different ways to improve gas mileage, so ArcelorMittal stepped up to the challenge. They came up with a way to produce a new type of steel that would improve fuel economy by reducing a vehicle’s weight.
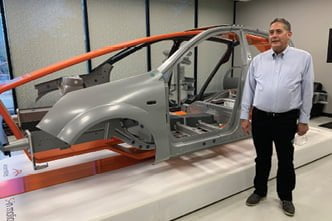
Automakers tried aluminum and other exotic metals, but they’re not always cost competitive.
“Steel is easily recyclable,” said David Price, group manager of automotive product development at ArcelorMittal’s global R&D site in East Chicago. “It’s the most recyclable material on the planet, but if we make it stronger, we can use less material.”
The steel needed to be thinner but still strong.
“Typically, it becomes less formable,” so tight corners and tight bends are difficult, Price said. The steels that were available then would crack or break more easily.
Developing a new steel is tricky.
“It’s kind of like making bread, and you don’t know how much ingredients you need and how long to cook it,” Price said. You might change the ingredients or the temperatures.
Price estimated it took 50 different experiments over 10 months to develop the new blend, working with the chemistry to get the atoms to align properly.
“It stretches a lot more, and you can bend it a lot easier,” Price said. “It’s called whole expansion, and if you punch a hole in a flat piece of steel, and you bend it into shape, what you don’t want is that it starts to crack around that hole.”
Price said it helps not only with parts that must be bent, but it helps in the die when you stretch a part because you don’t want dies to crack when you stamp it.
“As we got into it, and we had invented previous grades of steel that work,” Price said. The steelmaker then took the product to automakers.
The zinc coating for rust protection, combined with welds, made it very brittle. ArcelorMittal researchers had to figure out what was causing the problem and redesign the steel to combat that issue.
Price’s team redesigned the steel, changing the ratio of the different alloy agents.
“We’re the only ones in North America that make this material,” he said. “We’re the only ones, in the ArcelorMittal kingdom that spreads across the globe, that can make this material, and there’s nothing equivalent at this time.”
Designing the new steel wasn’t the end of it.
“We redesigned the chemistry of the steel, which also meant that we had to revamp our lines,” Price said. His team worked with an ArcelorMittal plant in Calvert, Alabama, a tiny town with just 609 residents, according to the 2020 Census.
“We spent a small fortune trying to get the line capable,” Price said. “We had the design ready about four years ago.”
He said the company had to wait until all the improvements were made.
“It took a couple years fixing things on the line to make it all work,” he said.
“Now we’re qualified and sole supplier for Ford and Chrysler,” Price said, for the 2021 Bronco and 2021 Jeep Cherokee.
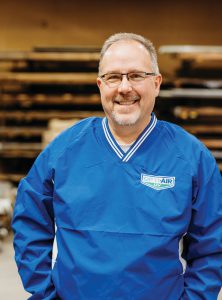
Air filtration
Tyson Foods gave Andrew Cleland a tight deadline for his award-winning innovation.
It was April 2020, and COVID-19 was devastating the meatpacking industry.
“They were losing people left and right,” Cleland said.
They were losing so many people that they would have had to charge customers almost double to add a second shift, sanitizing all surfaces between shifts.
Cleland is vice president of operations and head of product design at HD Industrial in Griffith. HD Industrial operates a custom fabrication shop with everything run by union sheet metal workers. Products include dust collection, air movement and a variety of other uses, from petrochemical plants to steel mills to various other clients.
Tyson reached out to Cleland and asked if he could develop something to help get rid of any kind of bacteria that is on all the surfaces of the building. The company needed the specialized equipment in seven days.
“They wrote me a purchase order I couldn’t refuse to come up with a seven-day prototype,” Cleland said.
Cleland created his first version, which had germicidal UV bulbs built into it.
“You can actually revolve the air in a given space,” he explained.
Petri dish tests showed Cleland was on the right track.
“They went through the entire unit,” he said, testing both before and after his air filtration unit was installed.
“They basically couldn’t believe what they were seeing,” he said. A meatpacking plant has blood spots, of course, which can hold a lot of bacteria. Cleland’s unit ran for 12 hours, and the bacteria count went from 1,400 parts per million to 100 PPM.
“They asked me if I could come up with a better streamlined unit,” he said. His company since has produced almost 1,000 units shipped all over the U.S.
“We have taken it, and we have gone to doctors’ offices, schools, hospitals” and more, he said.
The units are independent of HVAC systems for a reason. Furnaces and air conditioners cycle on and off. Cleland’s Opti-Air UV designs are always on to continuously filter the air.
A third-party testing company validated his product. It uses prefilters, UV bulbs and a final set of filters.
The company took the prefilters out, and they had trapped SARS, bacteria, mold and influenza.
The UV bulbs killed everything, he said, because the final filter didn’t find anything.
“It’s proven technology that we can move it through,” Cleland said. He’s developed a third prototype and is working on a fourth.
The third is a bigger industrial unit, handling 10,000 to 15,000 cubic feet per minute, which is a high volume of air. Generation four is a small cylindrical unit that could sit in a little area in a house.
A unit could be rolled into a room of a quarantined person with COVID-19.
“When the human takes the filter completely out of there, there’s no effect on them removing the filters with a pair of latex gloves, taking out the filter and dumping them into the trash can,” Cleland said.
Cleland emphasized the impact of his invention on improving lives.
One story he tells is about an employee with a minor heart problem who went to a workout room for therapy.
Exercising with a mask on isn’t the most fun thing to do, Cleland said. He created a unit that would circulate UV-treated air and help with surface contacts.
“It purifies, sanitizes the air in a gym,” Cleland said.
The units being produced now range from $3,600 to $25,000. Units for home use aren’t in production yet.
Aluminum framing system
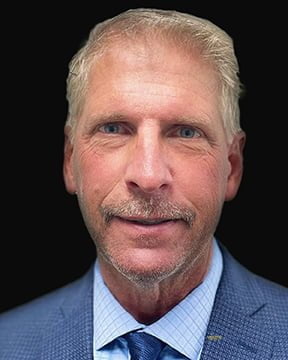
Roger Winter spent 37 years designing high- and midrise buildings in Chicago and other cities, working with the structure that holds the glass in place on the sides of buildings.
Among his designs was the Great Ape House at Lincoln Park Zoo, which had to be strong enough to keep silverback gorillas from going through it.
“I was never one to do all this cookie-cutter-shape stuff” with glass buildings, he said. Glass buildings, of course, have a lot of glass, but they also come with a lot of framing for support and to hold it all in place.
As president of Wintergreen Construction Co. in Crown Point, Winter is focusing on aluminum framework.
With the catastrophic collapse of wooden decks from rotted materials and other flaws, Winter developed DexSpan, an aluminum framing system that revolutionizes deck and dock structures. Unlike treated lumber, the aluminum won’t rot or twist or warp, he said. “We stay flat forever.”
Aluminum can be shaped and molded easily, too, for originality in designs.
“We design the dies kind of like Play-Doh molds,” Winter said, to extrude the aluminum.
Aluminum is about 40% lighter than wood and can span farther, too. Steel is strong, but when you cut or drill through steel, you’re supposed to paint it before using a screw to prevent corrosion, which isn’t necessary with aluminum, he added.
“I just started putting paper to pencil about six or seven years ago” and developed the DexSpan system, Winter said.
The DexSpan system was first used for residential decks but now is being used for amenity decks on commercial rooftops and for boat docks as well.
The amenity decks are in several downtown Chicago locations. They also are popular on the east and west coasts.
Winter included integrated handrail systems in the design. The fasteners are all concealed.
“It’s like an erector set how it fits together,” Winter said. “It goes in real fast, and it’s also lightweight.”
The first deck was 51 feet by 16 feet. Once the crew was trained, it was installed in under four hours with just a screw gun.
A wooden deck can take days to build.
“We’ve made many, many improvements since then,” Winter said. His team created an installation video to make DexSpan products easier to install.
Bishop Boxes

McKenya Dilworth’s innovation was kick-started by the pandemic. Her question: How can children do required art projects at home for virtual learning if they don’t have the necessary supplies?
“A lot of young people said, ‘Well, we didn’t have this. We didn’t have that,’” Dilworth, said. When lack of access to supplies deters learning, that’s a big problem.
“I love getting packages as an adult, and as a child, I loved getting mail — anything in the mail,” she said. That helped inspire Bishop Boxes, which contain materials necessary to complete lessons for a week or two.
Mailing the packages is expensive, though, and food distribution to students didn’t stop during the pandemic, so the Bishop Boxes were picked up along with the food.
“They were thrilled,” Dilworth said. “We had two weeks of activity in the box.”
Dilworth, executive director of the Morning Bishop Theatre Playhouse, named the boxes in honor of her mother, Morning Bishop.
The Bishop Boxes contained everything from paint-by-number kits to old magazines for collages. The old magazines proved popular.
One of the projects students did was to create a vision board.
“Use your imagination to manifest what you want in your life,” they were told. The students clipped photos and text from the magazines and added other material, along with “2021,” to construction paper.
“Do you want to graduate? Do you want to have a family? Do you want to have a career?” Dilworth ran through a list of potential abstract ideas. She said students enjoyed finding ways to show what they hoped to become.
Among the other projects was creating wind chimes.
“It was beautiful,” Dilworth said. “They understood the scientific element behind it.”
Students also put together race cars. Some of the students are virtual learners, but pupils attending school in person put tape on the ground and used their cars to study velocity, aerodynamics and other principles.
Bishop Boxes are still being used.
Dilworth said the parental support her students received is inspiring. The parents helped kids’ social and emotion dispositions as they stayed engaged with the arts.
“If there was a positive thing that came out of COVID-19, that was kids connecting with their families,” she said.
Click here to read more from the December-January 2022 issue of Northwest Indiana Business Magazine.