Education key to offering career paths in manufacturing
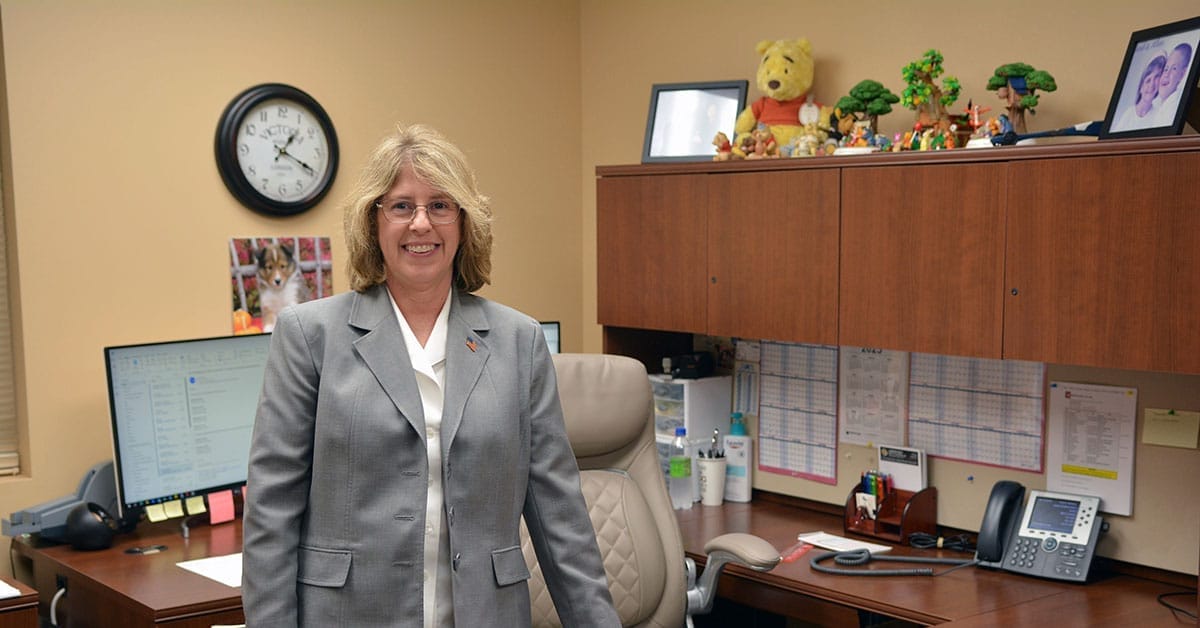
Shyann Cameron has always been a handy person.
“I’ve always liked just using tools. I used to call myself Barbara the Builder,” said the 36-year-old East Chicago resident.
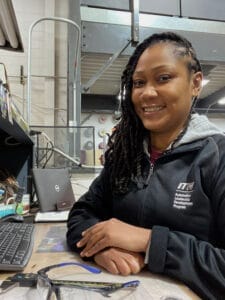
The mother of four boys, Cameron turned to manufacturing jobs because they paid better than working at fast food and other restaurants before making the switch.
“I had kids; they were smaller at the time,” she said. “In order to make money, I would have to work weird hours. I just didn’t have time for it.”
About a decade ago, she applied for a maintenance job at a company but didn’t get it. Cameron went to Ivy Tech Community College to learn machining and found a job as a machine operator.
About a year and a half ago, she found a new position as a tool maker with Illinois Tool Works in suburban Chicago.
“My job is to assess the problem of the mold and be able to trouble-shoot them, be able to repair them and use preventative maintenance to avoid any unexpected failures or costly downtime,” Cameron said. “I am basically repairing a mold machine.
“I am the first woman to work in this department ever.”
Women make up about 30 percent of workers in manufacturing, according to the U.S. Census Bureau.
U.S. manufacturing declined after the 2008 Great Recession but rebounded until the pandemic in 2020. The manufacturing sector grew by more than 11 percent between 2019 and 2023, according to the Deloitte Manufacturing Institute.
In fact, according to the institute, manufacturing employment has surpassed pre-pandemic levels and now stands at nearly 13 million as of January 2024.
This renewed upswing in manufacturing jobs doesn’t mean dirty, manual jobs.
Manufacturing employers, according to the Census Bureau, need a new kind of worker, one with skills to operate in a highly automated environment.
That means more opportunities for women.
Women like Cameron are seizing the moment. And, she said, her department has welcomed her.
“I wouldn’t say I feel intimidated. I would say that I actually get more help than I want sometimes,” Cameron said. “I definitely get a lot of encouragement from my fellow co-workers there.
“I work in a really good department so they’re always just challenging me to do things a different way or how to look at things a different way, and just showing me several different ways to do many things. It’s a lot of work. I’m still learning.”
She is one of the almost 354,000 women working in the trades, according to 2023 figures by the Institute for Women’s Policy Research.
Worth considering
Rosa Maria Salas is another one. She learned a lot from her decades in the steel industry — 44 years to be exact, first starting at Inland Steel Co., which is now part of Cleveland-Cliffs. She also served many years as a financial officer with the United Steelworkers of America Local 1010 in East Chicago.
A woman cannot let her femininity stand in the way of job opportunities and holding down a job.”
Before turning to manufacturing, she worked as a waitress.
“I was making $1 an hour as a waitress. At the time, I didn’t even know how to fill out an application,” Salas said.
Salas started her career in manufacturing in August 1978.
“This is when the steel mills were bustling. We were 60,000 (employees) strong,” Salas said.
Salas went on to work as a mechanic in the mill. Her time in the plant wasn’t without issues. She once fell 30 feet and broke her back.
She had to learn to walk again through a long and painful process.
Eventually, she returned to the mill to work as the first female band-saw operator, which basically allows you to cut steel to a specific length or width.
“It was a very simple job. It was just measuring, dropping the saw, cutting, bending it and putting it back in the bundle so they could go up to the customer,” Salas said. “I was the first woman. In fact, I think I’m the only woman that ever did that job because, after a while, the 12-inch bar mill shut down.”
Over her four decades in the mill, Salas had to endure the shuttering of departments and learning new positions elsewhere in the plant.
She finally retired in 2023 at the age of 70. She’s also a founding member of Women of Steel, a division within the United Steelworkers union.
Salas said working in manufacturing — including the steel industry — is something women should consider.
“It’s good because it creates opportunities to be trained,” Salas said.
However, Salas said some manufacturing positions can be physically challenging.
“It is physical. There is no going around it. It’s very physical,” Salas said. “When you go into labor, it’s all physical work and working in different environments, sometimes hot, sometimes cold. It takes a special person to be able to exist in an environment like that. But women should not be intimidated by it.”
One area of steelmaking, Salas said, dominated by women is working in what is called the “cold-strip” department.
“Cold strip is basically done by majority women now. There’s heavy equipment operating but you learn to use it.”
She has some advice for those thinking about a job in manufacturing.
“A woman cannot let her femininity stand in the way of job opportunities and holding down a job,” she said.
Slow going
Jeanne Robbins, the president of Munster Steel Co., is now in her 31st year with the company.
“When I first started, there were hardly any women involved in the industry. I would say there’s quite a few more now,” Robbins said. “But I’d still like to see more women joining.”
When Robbins started in the industry, men were less welcoming than they are today.
“I found myself as the only woman in meetings. Usually, one woman to about 12 men,” Robbins said. “Now I find myself not the only woman in a lot of things, but it’s been slow to introduce women to this industry.”
Munster Steel was founded in 1957 by O.C. Robbins as the OCR Steel Co. and later incorporated as Munster Steel Co. Inc. According to its website, the company began by fabricating structural steel, steel parts and iron.
“It has always been able to fabricate steel for both buildings and bridges and continues to do so in today’s market,” Munster Steel’s website states. “Led by Ms. Jeanne Robbins, third generation ownership, Munster Steel Co. Inc. continues to grow and push the leading edge of the steel fabricating industry forward.”
To attract more women in manufacturing, Robbins said recruiting needs to start in high school.
“They need to get more women involved in classes like detailing and manufacturing and shop and instead of just isolating them to the mathematics and cooking and sewing and things like that,” Robbins said. “I think that it needs to start young, and I think that the industry also needs to be more welcoming of them. I think that that would be the best way to just start young and get them more involved in high school and classes that would lead them down this path.”
Robbins said working in the shop can be intimidating for women, but there are other activities where they are needed and can excel.
“Welding does not require the physical strength that some of the other jobs in our shop would require,” Robbins said. “A lot of the women welders that I have known make excellent welders. I would really love to see more women going into the industry doing that type of work.”
Only 5.3% of welders are women in the U.S., according to the U.S. Department of Labor. A certified welder in Indiana earns an average of $22 an hour, according to ZipRecruiter. But, with experience, a welding engineer can earn an average of $77,344 a year nationwide, according to Payscale.com.
For females interested in pursuing a career in manufacturing, Robbins suggests they attend a trade school.
“I would recommend that they go to a trade school. I would recommend that they would go and learn about welding and get involved in that way. And then maybe go to the union hall and become an apprentice and learn the trade in that respect,” Robbins said.
Recruiting should start early
Leah Konrady reiterates that getting more females into manufacturing has to start at the high school level.
“We do a nice job of attracting students as they graduate from high school,” Konrady said. “I think the more students that are interested in the career path in machining or manufacturing should explore through their local high school how to get connected with employers that offer good manufacturing jobs.”
Konrady is CEO of Konrady Plastics. Her parents started the business in 1981 in Gary. The company moved to Portage in the late ’80s.
“We use plastics every day in our lives,” Konrady said.
One of the things I love about manufacturing is that every day is different. There is no same day in manufacturing.
Konrady said her company buys sheet or tube plastic, which it turns into parts for all sorts of items like for food processing equipment and conveyor systems.
Of its 32 employees, the company has several women working in its inside sales department and as a quality manager.
Konrady says recruiting women into the plastics industry is a priority, including for the trade association the company belongs to, the International Association of Plastic Distributors.
“They’ve created a whole section for women in plastics. It’s been one of the most successful programming events that the trade association has ever done,” Konrady said. “Its mission is to retain women into the industry and show a career path for women. It’s been widely successful.”
Konrady said the plastic industry is challenging but can be a rewarding career.
“One of the things I love about manufacturing is that every day is different. There is no same day in manufacturing,” Konrady said “The problems that come up every day are different.
“So, if you’re looking for a job with variety and constant problem solving, I think manufacturing is a wonderful place to go.”
Konrady said more needs to be done to promote machinist as a career path.
“Being a machinist is a professional career and a good career,” Konrady said. “I think we need to start early so students are looking at that as a career path, not just going to college. We have to remember that college is not for everyone.”
She said telling students about their options can lead to success.
“I think we need to do a better job of explaining the different career paths within the trades, including machining,” she said. “People assume that if you go into manufacturing, it’s gonna be a dirty workplace. It’s gonna be a harsh work environment.”
Not so at Konrady Plastics, which was recognized as one of the best places to work by the Indiana Chamber of Commerce in August 2024.
“I can share with you that Konrady Plastics is the exact opposite,” Konrady said. “We are a very, very clean shop.” •
Read more stories from the current issue of Northwest Indiana Business Magazine.