It can happen anywhere, and take inspiration from nearly anything.
by Mark Taylor
Innovation doesn't always begin in a laboratory. It can bubble up from a manufacturer's shop floor or rise from an office brainstorming session, or even be inspired by a mother's love for her ailing son. The 2013 class of inducted Fellows of the Society of Innovators of Northwest Indiana includes successful entrepreneurs and executives or owners of multimillion-dollar businesses, academics, professionals and scientists. It also includes a fabled group of decorated octogenarian World War II fighter pilots.
What they share is vision and a rare talent to diagnose and solve problems. Sometimes their efforts result in useful new products or unique ways to improve the world around us. The Society of Innovators of Northwest Indiana, which sponsors the awards, counts more than 300 teams and individuals as members. From that group, individuals and teams are nominated and finalists selected to be honored as Fellows or awarded the Chanute Prize for Innovation.
“The judges are dedicated to the proposition that innovation is important to the future of Northwest Indiana and they're willing to invest their time because they have a passion for encouraging innovation across all walks of life,” says John Davies, assistant director of the Gerald I. Lamkin Innovation & Entrepreneurship Center at Ivy Tech Community College Northwest, which sponsors the Society.
“Anyone can be an innovator. And what we've discovered is that innovation is more prevalent than people think,” says Davies, who serves as the Innovation Society's managing director.
Six individuals were inducted as Fellows and two teams shared the Chanute Prize for Team Innovation at a ceremony at Hammond's Horseshoe Casino on Oct. 17. The Society is a project of the Gerald I. Lamkin Innovation and Entrepreneurship Center of Ivy Tech Community College Northwest.
The Society of Innovators is helped by principal partners ArcelorMittal, Bukva Imaging, Doherty Imaging, Horseshoe Casino, Krieg DeVault, NIPSCO, Northwest Indiana Business Quarterly and the Times Media Co.
Nominations are submitted annually from Jasper, LaPorte, Lake, Newton, Porter, Pulaski and Starke counties.
Gerald I. Lamkin Fellow for Outstanding Achievement in Innovation and Service
Stewart McMillan, President & CEO, Task Force Tips, Valparaiso
Stewart McMillan, the 2013 winner of the Gerald I. Lamkin Fellow for Outstanding Achievement in Innovation and Service, believes that innovation can be taught. More accurately, he says, the word is “nurture.”
“You must nurture a climate that is supportive of creativity,” explains McMillan, the president and CEO of Task Force Tips in Valparaiso, one of the world's leading producers of fire department equipment. “Not every idea is a good one. Ideas come out of something like a rock tumbler. You add rocks, soap and water, put them into a tumbler and when they come out, they're polished. I love that metaphor: people rubbing against each other and playing off their ideas. It just takes the tiniest spark to light a fire. When you have people playing off each other, that spark turns into a blaze and then an inferno. Everybody in the room gets energized by what they can do with each other.”
And by using tools such as collaborative software programs, a company blog and changing the dynamics for new product development, McMillan has created an environment that he says encourages Task Force Tips employees to be innovators and participate in new product design.
McMillan was the first full-time employee in a company started by his father, Clyde McMillan, in their family's Hobart basement more than 30 years ago. He says Task Force Tips starts to foster a climate of innovation by opening the channels of information company-wide.
“That's what we do with employees,” he says. “You never know what question they will ask that will spark an idea. You have to teach people to be alert to listen and accept any idea as OK and not crush it, but look to see where it leads. Don't tear ideas down. Accept and celebrate failure, because you learn from every failure. Leadership's job is to make sure this happens and is not just talked about.”
An example of how that plays out at Task Force Tips is by now company lore.
“King Arthur didn't sit around with the knight at the ‘boat-shaped table.' It was a round table,” he explains.
“We used to have a conference table that was boat-shaped. People moved and sat in different places around the table and I did an experiment to see where they sat. It was clear that they were uncomfortable sitting at the end of the table,” he says. “So one year ago, we ripped out the conference table and custom-built a 14-foot round table so everyone would feel equal. Everyone already knows where the power is, who the president is. But if you put yourself at the end of the table, you're lost before you get started, because you put yourself in the position to crush any idea.”
TFT's primary customer base is fire departments, mostly municipal, although many serve private employers. TFT also serves military and commercial aviation clients. He says the company's focus is delivering products that make firefighters safer and more efficient. About 45 percent of TFT's fire and aviation equipment is sold globally, with annual sales approaching $40 million.
McMillan says he's tired of hearing that American manufacturing is dead.
“We are still the world's largest manufacturer and we're becoming more efficient. We're automating, producing more products with fewer jobs. It doesn't mean manufacturing is dead. On the contrary, American manufacturing is growing dramatically. The cheap labor advantage of poorer countries will disappear,” he predicts. “And American innovation will come out on top.”
Fellows
Julie Bombacino, entrepreneur, founder and president, Just Food Blends
Julie Bombacino of Chesterton believes the old adage that necessity is the mother of invention. When her second child, A.J., was born with a brain malformation that caused repeated seizures, he was unable to chew and swallow food without aspirating and vomiting.
A.J. became one of an estimated one million Americans who require regular tube feedings that bypass the mouth and taste buds and go directly into the stomach.
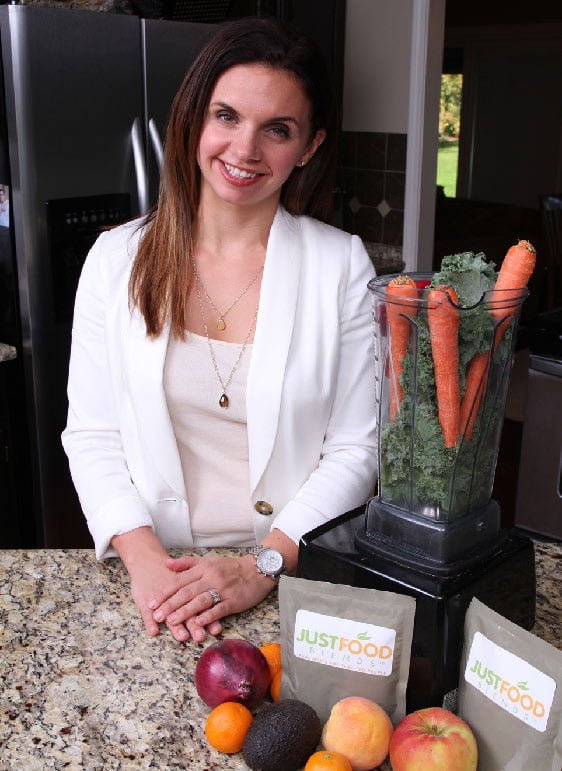
However, when Bombacino fed A.J. the commercial feeding tube formulas, he had trouble digesting them. So, like many mothers of special-needs children, she searched the Internet for answers and found a “tribe” of caring parents and spouses of people who need tube feeding. Many offered helpful suggestions about blending fresh fruits and vegetables, fish and meats to offer nutritious meals for their loved ones.
“My son was not gaining weight,” she remembers about A.J., now 2 1/2 years old. “He'd tried eight different formulas before I started blending real food for him, and that made a world of difference.”
Bombacino says the daily vomiting stopped almost instantly and A.J. was able to go to the bathroom on his own after months of constipation. “His skin color returned and he grew really well and fast on the food blends.”
Then the light bulb flicked on, and in 2012 Just Foods was born.
Bombacino learned that the nearly one million Americans requiring tube feeding consume almost $3 billion annually in commercial formulas, formulas she said deliver little nutritional variety and often contain up to 50 percent corn syrup.
So she began experimenting, creating recipes for meals prepared with all natural, real foods for A.J., her firm's “Chief Inspiration Officer.”
“It's been a blessing to get him good nutrition,” she says. “But it isn't easy and traveling with fresh foods and a blender is challenging. It would be nice to have a convenient food option for him. We are trying to give people on feeding tubes access to real food with nutritional variety.”
Bombacino says she believes Just Food is the first shelf-stable blended real food product for tube feeding. Her three real food meal options are processed at high heat and vacuum-sealed in plastic pouches to provide healthy options to commercial formulas. Bombacino says she raised capital to launch her company and found a firm in Oregon that agreed to produce her products, slated for release by year's end. She plans to deliver them to dietitians and nutritionists in hospitals and nursing homes to reach tube-feeding patients there and develop customers in those key market segments.
“Our goal is to demystify the idea of using real food in a feeding tube,” she says. “Having these real food pouches as an option will help the families of people with feeding tubes.”
Mike Falk, PE, LS – Founder and Owner, Falk PLI Engineering and Surveying, Portage
Falk-PLI Engineering and Surveying Co. was among the first to introduce fast, sophisticated and accurate new surveying instruments such as laser trackers and laser scanners to the steel industry. Founder Mike Falk says the new precision industrial alignment tools and his trained and experienced staff have helped steel mills locally and nationally to become more efficient and productive. The company now operates satellite offices in Mobile, Ala., and Pittsburgh, Pa., and is headquartered in Portage.
In a recent local news story, Indiana Gov. Mike Pence lauded Falk's firm, noting: “The success of innovative companies like Falk-PLI is proof that Hoosier ingenuity, paired with a prosperous business climate, can foster dramatic growth.”

Falk says laser trackers are replacing older methods of measurement and have freed his staff to examine problems differently. “The technology alone doesn't solve the problem. It's the people. Many others have failed with new technology because they haven't freed themselves from the old technology methods and old approaches to problem solving.”
He says before the introduction of lasers, engineers and surveyors could take three camera shots in 15 seconds.
“Now we can take 150,000 shots in 15 seconds and the laser scanner can take 15 million shots. What is all that extra data trying to tell us? That everything in the world moves. But precisely how, when, where and by how much is what's valuable to know.”
He says the new technology sometimes reveals structural and alignment problems that steel company executives were unaware of. “We changed how to attack the problems.”
For example, Falk-PLI consults with steel companies to provide alignment services when a new facility is being built. He said most of his clients cannot afford to buy and install new production equipment and must rely on older machinery. “We show them that they don't always have to replace that equipment, but can improve its use and extend its life to become more efficient. We want to be a part of the solution.”
Falk-PLI owns 13 lasers and six laser scanners.
Falk, 52, a Bluffton native and Purdue University graduate, moved to Northwest Indiana with a gentlemen's agreement to purchase a local engineering firm that hired him as a general manager. He was fired 18 months later.
“I cried in my beer, got back on the horse and launched Falk-PLI from my basement,” he recalls. The mark of an innovator, Falk says, is epitomized in his company credo: “You just have to keep trying.”
Nina Fonstein, Ph.D., retired scientist, now consulting for ArcelorMittal Global Research & Development Center, East Chicago
Innovate or die. That's the dilemma facing the U.S. steel industry.
“It is a point of survival,” says Nina Fonstein, Ph.D., one of the world experts on the “new steels.” “It's no secret that there is huge competition in the steel industry. Some companies are facing big problems. To survive, every steel company has to increase the market share for its products. It's vital for them to be better than their competitors. The new steels we are developing are a big part of this competitive edge.”
She says that new generations of cars will require breakthrough steels that are both lighter and stronger. And the American steel industry's ability to respond to those challenges has been aided by Fonstein and her team at ArcelorMittal.
Richard Sussman, Ph.D., Fonstein's former boss and retired general manager of ArcelorMittal's Global R&D Center, calls her “a pioneer among a generation of pioneers in different countries who helped introduce the so-called ‘new steels' to the global steel industry.”
Sussman says Fonstein has been a scientist and technical manager in the steel industry for more than 45 years in Russia and the United States. She is a world-recognized expert in sheet formable steels for the automotive and agricultural industries; long products for cold heading of fasteners; and hot forging and high-strength low alloyed steels, especially for gas pipelines.
Today those steel products are commonplace, allowing car manufacturers to produce lighter-weight vehicles that consume less fuel, are more energy efficient and create fewer carbon emissions. They also protect passengers better because of the increased steel strengths.
Fonstein, who wrote the world's first book on the “dual phase steels” in 1986, says she couldn't imagine then that steel could approach this level of strength, more than three times stronger today than in the '80s.
“The steel industry appears to be capable of creating strengths with properties we previously thought impossible,” she says. “It's difficult to imagine how big this evolution has been in the steel and auto industries.”
From 1998 until her 2011 retirement she led the automotive steel product development group for what is now ArcelorMittal in East Chicago. Fonstein, who earned two doctorate degrees in the former Soviet Union in solid state physics and physical metallurgy, was awarded 20 patents in Russia and three in the U.S. Her reputation spread internationally with the publication of “Low Alloyed Dual-Phase Steels.”
She headed the laboratory of the I.P. Bardin Central Research Institute in Moscow from 1973-1998, when she left Russia. “We had to be innovative or die. Many research centers lost a lot of people, but we survived because we were the best,” says Fonstein, now a consultant with ArcelorMittal. “Innovation is always part of my daily work.”
Lisa Hopp, Ph.D., RN, Purdue University Calumet, founding director of the Indiana Center for Evidenced-Based Nursing Practice
In 2004 Lisa Hopp observed a vexing problem: a gap in the knowledge level of nurses about what constitutes the best nursing practices. While the evidence-based medicine movement was growing worldwide, finding which practices worked best was harder in nursing.
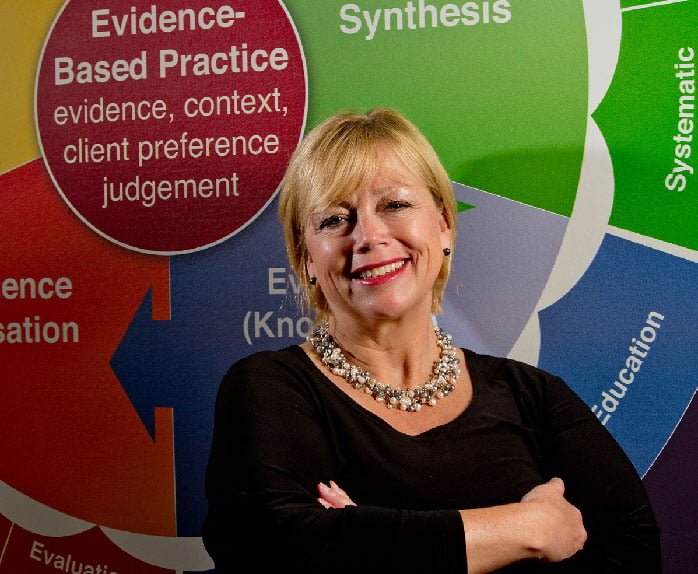
Hopp knew that nurses spend more time with hospital and nursing home patients than physicians and have great potential to improve the quality of patient care and outcomes. Yet there were no U.S. academic or research centers for evidence-based nursing practices.
“I was focused on decisions that nurses make independently, finding the best evidence to support the kinds of things we needed to do and teach our students to do.”
Then she discovered the Joanna Briggs Institute (JBI) of the University of Adelaide, South Australia. JBI is a global collaborative to promote the synthesis, transfer and utilization of evidence through effective healthcare practices to improve healthcare outcomes.
Hopp had found her mission. She soon learned that JBI was planning to launch six centers worldwide. She went to her school's dean, Peggy Girard, to elicit support for Purdue University Calumet to become one of those centers.
“We agreed that we had the pieces in place and could assume a leadership role. PUC is a regional campus whose main mission is to teach,” Hopp says. “We are not a research-intensive facility. This fits our mission, not to perform primary research, but to synthesize the research that exists, and help in transferring and implementing it.”
Eighteen months later Purdue Calumet's Indiana Center for Evidence-Based Nursing Practice became the only such center in the Midwest, serving as a resource for nurses and hospitals in more than one dozen states and integrating the best evidence-based practices into Purdue Calumet's nursing courses.
Hopp says the center led to opportunities for training nurses, disseminating best practices and improving patient outcomes at hospitals throughout Northwest Indiana and Chicagoland through a program called the Evidence Implementation Fellowship in May 2012.
That program brought together quality leaders, staff nurses and clinical nurse specialists from nine hospitals in Northwest Indiana and Chicago for a one-week boot camp. Teams identified specific hospital goals, such as reducing hospital readmissions for chronic heart failure patients, eliminating bed sores, preventing falls or cutting catheter-associated infections in their hospitals. The center offered help in implementing the best evidence-supported practices, and data analysis and problem-solving support.
“All nine teams were successful. And some did some truly amazing things in improving outcomes,” she says. The program has improved patient care, for example, dramatically reducing patient readmissions for chronic heart failure patients at a LaPorte hospital and reducing catheter infections at several participating facilities.
“These conditions can cost hospitals a lot of money and sometimes peoples' lives,” she says. “If you can avoid these catheter infections and reduce readmissions, you can recoup costs very quickly. In the future we need to point out improvements in return on investment, because you don't have to even have amazing clinical results to achieve an improved return on investment.”
Don Keller, president and CEO of Tri-State Industries, Hammond
Growing up, Don Keller must have liked “The Jetsons.”
Like the iconic 1960s cartoon show, Keller envisions a world in which technology is used to improve the lives of Americans, particularly small manufacturers seeking a competitive edge. His new division, Tri-State Automation, is the first in Northwest Indiana and the Chicagoland area to refurbish and sell used robots to local manufacturers, one of only a handful nationally.
The Lake Village resident has been building a better mousetrap for 33 years at his firm's parent company, Tri-State Industries, which operates five divisions in three buildings in Indiana and Louisiana. Tri-State produces rail car parts for Union Tank Co., welding trailers for several firms and through its JD Steel, operates a steel service center that buys bulk steel and cuts it to size.

Years ago Keller embraced the “Lean Manufacturing” continuous improvement process championed by Toyota and employs it throughout his businesses. Lean is a team-based approach to problem solving that requires supervisors to work closely with other staff to improve safety, cut waste and improve efficiency.
Twelve years ago Keller purchased robots that now perform many of the welding operations and recognized a broader business opportunity. He says when Tri-State adopted robotics, the company found it difficult to locate vendors to help with maintenance, tooling and programming.
“As we struggled, we figured others were in the same boat. The big companies can afford to purchase new robots for up to $200,000, work them for five or six years, then replace them with new ones. Small companies cannot. So we started a new division, Tri-State Automation, which offers training, technical support and programming, and purchases and refurbishes used robots.”
Keller says the 2-year-old automation division applies 30 years of manufacturing experience to its robotics clients.
“When we looked at robotics we saw that robotic welders can work two to four times faster than a human being. Their productivity is off the charts and they don't get sick from exposure to smoke,” he says. “And quality improves. It's one of the most radical things any small company can do, the next big leap into technology.”
He says most robots aren't used for welding, but perform material handling, stacking and closing boxes or doors. “Welding robots comprise only 10 percent to 20 percent of the market, but will grow as it becomes more affordable,” Keller says. “We believe robotics will lead to a renaissance in American manufacturing.”
Co-Recipients, Chanute Prize for Team Innovation
The Chicago “DODO” Chapter of the Tuskegee Airmen Inc., Ken Rapier, chapter president
The co-recipient of the 2013 Chanute Prize for Team Innovation is not a scientific research team or technology wizard. But the Chicago “DODO” Chapter of the fabled Tuskegee Airmen knows something about teamwork and innovative thinking.
The Airmen, highly decorated African-American pilots who battled discrimination even as they fought bravely during World War II, is awarded the Chanute Prize for its Young Eagles Aviation Program. The Chanute Prize is named after French aviator and innovator Octave Chanute, whose 1896 flights along the Indiana Dunes paved the way for the Wright brothers and the growth of aviation. The Chanute Prize is co-sponsored by Krieg DeVault Law Firm, NIPSCO and Ivy Tech Community College Northwest.
The Chicago chapter of the Tuskegee Airmen launched its Young Eagles aviation program for Chicagoland youth at the former Chicago Meigs Field in 1994. Since then more than 14,000 youths have enjoyed free flights intended to encourage careers in aviation. The monthly program, which is operated in conjunction with the Experimental Aviation Association, moved to the Gary/Chicago Airport after Meigs Field was closed in 2003. The Young Eagles program also offers follow-up flight training and educational opportunities and mentoring to youths ages 8 through 17 interested in aviation. The flights are scheduled the second Saturday of the month, weather permitting.
“This is one of the best-kept secrets in Northwest Indiana,” says Ken Rapier, 65, a Chicago pilot, flight instructor and president of the Chicago Chapter. Rapier was the first non-World War II pilot allowed to join the Airmen. He says the Young Eagles program goes beyond the free flights, which he says excite the imagination of young people of all races.
“The program also offers youngsters an opportunity to meet and interact with the original Tuskegee Airmen, some of our legends of history, who come when they're able. The Tuskegee Airmen stand for education and assisting young people,” Rapier says.
Youths expressing strong interest in aviation after taking the flights become eligible for an online private pilot course, which they can take free of charge. And every year at least one youngster over 16 who has successfully completed that online pilot course receives a private flight training scholarship to obtain a pilot license. Other programs include a one week aviation youth program every summer at O'Hare and its Legacy Flight Academy to further pilot training.
Rapier says the chapter name “DODO” was adopted tongue-in-cheek by the Tuskegee Airmen after the extinct bird that lost its ability to fly. He says after proving their skill and valor during World War II, the pilots were often denied the opportunity to fly commercial aircraft because of their race. And like the dodo, seemingly lost their ability to fly.
He conceded that time is thinning the ranks of the Tuskegee Airmen. The 12 local surviving chapter airmen are between 87 and 93. “We're losing them at much too rapid a rate,” he says. “Theirs' is a story that needs to be told and we're trying not only to preserve that legacy, but to continue it,” says Rapier.
Kemin Food Technologies Inc., Des Moines, Robert Stomp, director of operations, and Edward Lambert of Lambert Farm, North Judson
This year's other Chanute Prize for Team Innovation co-recipient is responsible for creating, farming, harvesting and processing a new breed of spearmint that contains an antioxidant able to preserve the color, freshness and shelf life of foods.
Kemin Food Technologies, a family-owned agricultural products company based in Des Moines, Iowa, partnered with third-generation Starke County farmer Edward Lambert to grow this uniquely propertied plant. These patented strains of spearmint produce an all-natural extract that replaces artificial products used to delay color and flavor loss and deterioration in human and animal foods.
Robert Stomp, Kemin's director of operations, says the project began in 2007 in the greenhouse stages and the first real crops were harvested in Starke County fields in 2012.
The commercial product, known by its brand name of Fortra, is a potent antioxidant known in the industry as a botanical extract. In 2012 Lambert Farms produced 80 tons of the spearmint extract on 225 acres and in 2013 Stomp says the farm doubled acreage and doubled capacity. Stomp says the water-soluble product can be used in vegetable oils, dairy beverages and products such as ketchup, as well as pet foods.
“The market for food antioxidants is enormous,” Stomp says. He says that Kemin's first challenge was finding the right farmer partners, locations and agronomic practices.
“This isn't for people who aren't entrepreneurial. This isn't a publicly traded commodity like corn or soy. We worked together on the growth part. We were developing plant lines that would require great heartiness and survivability and weren't susceptible to plants or insects,” he says.
Edward Lambert Jr. is a third-generation family farmer who, with his brothers, Dave and Chris Lambert, raises corn, soybeans, peppermint and spearmint on more than 3,000 acres in Starke County. Lambert says Kemin worked through the Indiana Mint Market Development Council, a trade group for mint farmers, to recruit farmers to plant, nurture and harvest the patented spearmint plants. He says the Kemin plants are distinctly different from other spearmint he's grown whose oils are used by such companies as Wrigley and Colgate.
He says several other local mint farmers were approached by Kemin, but refused the opportunity to plant the new product.
“I'm the type of guy to take a challenge. That's what it boils down to,” he says. “Some people are happy with the status quo. But some like me are looking for the next new product. Now we have our process working well and we're ending our second full year. We've proven that this works.”